In this case the foam will be destroyed, so that is much better than the polystyrene making it's way to land fill. The sustainable aspect of the project is more about engaging with a manufacturing process and the possibilities it opens. It is then about taking aluminium and actually recycling it (rather than chucking it in a recycling box and sending it out of mind) into useful and desirable objects.
Hopefully by engaging in this process people (however few) begin to appreciate the process and difficulties encountered by designers and manufacturers alike. I hope that people discover the joys of making as much as anything.
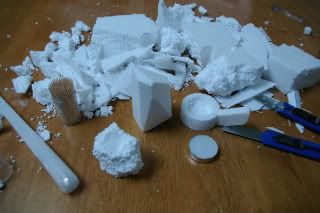
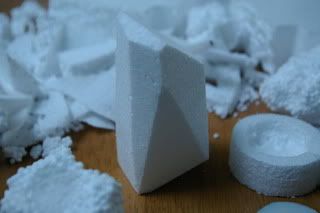
I did some foam studies, as you can see above. Although this was a hugely enjoyable process, the way I did it (using just my fingers, using a craft knife and using a hole-saw and a craft knife) produced a lot of waste.
Max Lamb, Chris Kabel,Reddish and Tom Dixon have all used the lost foam casting process.
Max Lamb has really worked with the process himself, and this deep and intimate understanding of the process seems to be his motivation. His pewter sand casting video is lovely, and a really nice twist on the sand casting process. With the polystyrene chairs and for the Dove table by Reddish, I would imagine a lot of waste polystyrene produced in making the originally forms. This is something want to avoid in this project.
Max, Reddish and Chris Kabel also exploit the nature of the polystyrene ball construction by reinterpreting this in the moulded material, be it pewter, aluminium or gold. The project by Tom Dixon seems to be a faster more visceral attempt to use blocks of foam to make metal furniture and products. These objects seem more naive and less refined than the other designers, and the painted finish disguises the properties and aesthetic of both the foam and cast metal.
I don't want to replicate the aesthetic of the foam. My aim will be to try and produced a cast or series of castings that attain a more refined and engineering driven aesthetic. This will also assist in producing the minimal amount of polystyrene waste.
As I am also limited by size, the castings will be relatively small, making them easier to produce and cast(hopefully).
These are the key differences to the projects above as I see them.
(a) I have made my own furnace, which can be made by anyone with a moderate amount of skill and patience, to smelt aluminium and produce the castings.
(b) The polystyrene moulds will be designed and made with minimal waste.
(c) The polystyrene moulds will be made from waste and found material.
(d) The aluminium used will be scrap and found material, such as drinks cans.
(e) The aesthetic of the castings will be driven by engineering and function.
(f) The castings will be small and easy to reproduce.
Disclaimer: This is a DIY project and Chris Jackson takes no responsibility for any injury,accident, loss or damage should you choose to engage in a similar project after reading this blog. In this, or any similar project, due care and diligence should be taken and always wear the proper safety equipment and take relevant precautions. If in doubt consult an expert or trades person.
No comments:
Post a Comment